In Halle hat sich die ThermHex Waben GmbH mit einer innovativen Wabentechnologie etabliert. Kunden profitieren vor allem von erheblichen Kosten- und Gewichtseinsparungen sowie sparsamen Ressourceneinsatz.
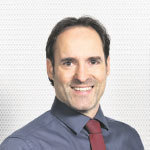
Dr. Jochen Pflug
Geschäftsführer ThermHex Waben GmbH
In Ihrer Firma ThermHex Waben läuft eine kleine Revolution vom Band. Was ist das Besondere an Ihrem Material?
Mit unserer patentierten ThermHex-Technologie gelingt es uns erstmalig, thermoplastische Wabenkerne in einem kontinuierlichen Produktionsprozess herzustellen.
Wie wurden Wabenkerne bisher produziert?
Bislang waren Wabenkerne relativ teuer, aufwändig und in vielen einzelnen Schritten herzustellen. Sie konnten die Kombination aus Kosten- und Gewichtseinsparung, die Kunden in vielen Industriezweigen heute fordern, nicht erfüllen.
Wie produzieren Sie dagegen Wabenkerne?
In einer einzigen Produktionslinie werden thermoplastische Polymere zu einer Folie extrudiert, vakuumgeformt und zu einem Wabenkern gefaltet. In dieser Produktionslinie können direkt mit der Herstellung des Kerns Decklagen auf die Wabe laminiert werden. Diese Decklagen können Vliesstoffe sein, für die Verklebung von Faserverbunddecklagen mit duromeren Harzsystemen oder direkt Decklagen aus themopastischen Folien bzw. Faserverbunwerkstoffen-, Aluminium oder Stahl.
Unser Prozess ermöglicht die Produktion von Wabenkernen mit drei bis 30 Millimeter Dicke und einer individuellen Länge bis zu sechs Metern mit einer Geschwindigkeit von bis zu zehn Metern pro Minute. Die ThermHex Wabenkerne haben eine zur Hälfte geschlossene Oberfläche, was eine optimale Verbindung zwischen Kern und Decklagenmaterial ermöglicht.
Möglich ist außerdem, die Wabenfertigung in einen bestehenden Herstellungsprozess für ein Sandwichplattenmaterial in eine durchgehende Produktion zu integrieren. Das führt zu weiteren Kostensenkungen und verbesserter Produktqualität.
Wofür sind Ihre Wabenkerne einsetzbar?
Das Material wird für Verkleidungen für LKW und Busse, Wände für Fertigbäder, Aufbauten für LKW-Anhänger, verschiedenste Faserverbundbauteile sowie Interieur- und Strukturbauteile für Fahrzeuge oder Yachten verwendet.
Auch komplex geformte Bauteile wie Gondelverkleidungen von Windkraftanlagen sind möglich. Durch die geringen Kosten ist das Material sehr interessant für kostensensible Industrien, zum Beispiel die Verpackungs-, Möbel- und Automobilindustrie. Auf Grund der sehr dünnen Wabenkerne von 3,5 Millimetern können auch dünne Faserverbundbauteile durch Sandwichbauteile ersetzt werden.
Von welchen Vorteilen profitieren Ihre Kunden?
Sie haben maximale Kostenreduktion und maximale Gewichtseinsparung bei minimalem Materialeinsatz in einem Produkt. Vereint in einer kontinuierlichen Produktionslinie. Die thermoplastischen Wabenkerne sind außerdem vollständig recycelbar. Alle bei der Produktion anfallenden Reste führen wir sofort wieder dem Produktionskreislauf zu. Unser Rohstoff Polypropylen wird aus dem nahegelegenen Chemiestandort Leuna bezogen, so dass der logistische Aufwand minimal ist.
Wo ist der Sitz Ihres Unternehmens?
Wir haben unseren Standort in Halle in Sachsen-Anhalt, wo Faserverbundmaterialien und Leichtbau Schlüsseltechnologien sind. Es ist kein Zufall, dass wir uns hier niedergelassen haben. Im Jahr 1901 entwickelte die Papierwarenfabrik Heilbrunn & Pinner hier das patentierte Verfahren für expandierte Papierwaben.
So kehrt die Idee, die damals zunächst für dekorative Papierwaren gedacht war, an ihren Geburtsort zurück – nur durch unser ThermHex-Verfahren eben weiterentwickelt und angepasst an die Anforderungen des modernen Leichtbaus. In 2014 sind wir vom Land außerdem mit dem Hugo-Junkers-Preis ausgezeichnet worden. Hugo Junkers hatte 1915 die Sandwichbauweise mit Wabenkern für Flugzeuge entwickelt und patentiert.
Wie sind Sie als Unternehmen aufgestellt?
Wir sind eine hundertprozentige Tochter der belgischen Firma Econcore, die sich ausschließlich mit Forschung und Entwicklung im Leichtbau beschäftigt. Wir produzieren seit 2010 in Halle auf nun 4500 Quadratmetern.
Im Dezember 2015 haben wir unsere Produktionskapazität durch einen neuen Extruder mit deutlich höherem Durchsatz vergrößert. Dadurch wird es nun möglich den Ausstoß an Wabenkernen nochmals zu verdoppeln.
Was reizt Sie persönlich an Wabenkernen?
Wir wollen dass Wabenkerne überall da, wo sie Gewicht reduzieren, auch Kosten einsparen und unsere Kunden darin unterstützen, die wachsenden Anforderungen zur Gewichtsreduktion und dem schonenderen Umgang mit Rohstoffen zu erfüllen.
Wir sind fest davon überzeugt, dass sich durch den Einsatz kostenoptimierter kontinuierlicher Produktionstechnologien die Kosten für Leichtbaumaterialien so reduzieren lassen, dass diese in immer mehr Anwendungsbereichen Umweltbelastungen reduzieren können und eine verbesserte Nachhaltigkeit des Wirtschaftens erreicht werden kann.