Digitale Zwillinge werden die Fabrik der Zukunft bestimmen. Ihr zentraler Vorteil: Als digitale Abbilder können sie im Internet der Dinge unterschiedliche Informationen für verschiedene Zielgruppe an einem Ort bereithalten.
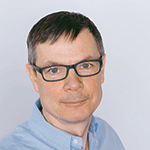
Steffen Himstedt
Geschäftsführer bei Trebing + Himstedt
Geräte, wie zum Beispiel ein Getriebe, eine Pumpe oder ein Filter, lassen sich so mit einem digitalen Zwilling in einer Cloud darstellen. Auf dieses Netzwerk greifen verschiedene Teilnehmer zu: Der Hersteller, der Nutzer und ein Servicepartner haben dabei unterschiedliche Interessen, die der digitale Zwilling wie auf einer gemeinsam genutzten Businessplattform bedient.
Ein Zwilling, mehrere Sichten
Der Hersteller erfährt auf diese Weise, wie der Nutzer sein Produkt verwendet. Außerdem kann er dafür über den digitalen Zwilling die notwendigen technischen Informationen bereitstellen. Praktischerweise könnte das Gerät so gleich mit einem Komponenten- und Ersatzteilkatalog verknüpft sein. Tritt der Wartungsfall beim Nutzer ein, kann er schnell die Originalteile nachbestellen. Schon kommt der Servicepartner ins Spiel, der ebenfalls über den digitalen Zwilling Zugriff auf Prozesse hat.
Auf dieser Plattform sind dann also auch mehrere Produkte des Herstellers zu finden. Hersteller wie Servicepartner können hier sämtliche Daten der jeweiligen Modelle für den Nutzer zur Verfügung stellen – und das über den gesamten Lebenszyklus. Möglich ist auch, Ansicht und Rechte exklusiv zu vergeben, um bestimmten Sicherheitsanforderungen gerecht zu werden. Beispiel: Ein Pumpenhersteller stellt seine Pumpe mit Daten wie den Ersatzteilen im Netzwerk bereit. Dort hält er sie auf dem neuesten Stand. Gleichzeitig informiert er hier über Neuigkeiten wie Software-Updates. Ein Chemiepark als Nutzer bindet diese Pumpe in seine Sicht des digitalen Zwillings ein. Dann ergänzt er seine individuellen Daten zur Performance, die über Sensoren gesammelt werden, zum Beispiel den Stromverbrauch für den Pumpvorgang. Veränderungen im realen Produkt können also gleichzeitig in seiner virtuellen Kopie dokumentiert werden.
Zentrum für Zusammenarbeit
Der Servicepartner wiederum bekommt seine Dienstleistersicht auf die Dinge: Neben regulären Wartungsintervallen können es auch vorausschauende Parameter sein. So ließe sich eventuell aus dem steigenden Stromverbrauch ablesen, dass die Pumpe bald eine Wartung benötigt, damit sie nicht ausfällt. Notwendige Ersatzteile können direkt über das Netzwerk bestellt werden, da der Hersteller bereits angegeben hat, welche Ersatzteile für diese Pumpe passend sind. So verbindet der Zwilling auch hier alle drei Partner wie in einem Zentrum für effizientere Zusammenarbeit.
Integriertes Management
Mit diesen Vorteilen kommen jedoch weitere Herausforderungen hinzu: Der digitale Zwilling wird mit zunehmendem Alter – oder fortschreitendem Lebenszyklus – immer umfangreicher. Er gewinnt durch neue Daten an „Masse“. Die Historie dieser Daten macht ihn dabei auch wertvoller und ist letztlich die Voraussetzung für neue digitale Anwendungen und Geschäftsmodelle. Diese Wettbewerbsvorteile werden jedoch ohne ein integriertes Management des digitalen Zwillings nicht zu erreichen sein.
Denn wer eine smarte Fabrik auf diese Weise mit dem digitalen Zwilling aufbauen möchte, muss ihn über den gesamten Lebenszyklus entlang der Wertschöpfungskette hinweg managen. Zu viele integrierte IT-Systeme führen dabei zu Inflexibilität. Es braucht daher künftig immer ein integriertes, leistungsstarkes Backend. Erst darauf aufbauend können Unternehmen die vielfältige Welt der Apps und ihrer dahintergeschalteten Dienste, Produkte und Geräte leicht und effektiv für ihre smarte Fabrik nutzen.
Die sechs Phasen der digitalen Transformation
Ein Gespräch mit Steffen Himstedt, Geschäftsführer bei Trebing + Himstedt, über die Frage, wie Unternehmen ihre Produktion in der digitalen Transformation effizient gestalten können, und ein erfolgreiches Sechs-Phasen-Modell für einen strukturierten Prozess dahin.
Ein Gespräch mit Steffen Himstedt, Geschäftsführer bei Trebing + Himstedt, über die Frage, wie Unternehmen ihre Produktion in der digitalen Transformation effizient gestalten können, und ein erfolgreiches Sechs-Phasen-Modell für einen strukturierten Prozess dahin.
Als Berater sind Sie häufig in deutschen Unternehmen – wie nehmen Sie die Firmen bei diesem Thema wahr?
Obwohl viele selbst als Hidden Champions innovative Spitzentechnologie produzieren, sind sie bei der Digitalisierung noch zögerlich. Viele haben Berührungsängste. Ihnen fehlt der Überblick über mögliche Ziele und verfügbare Technologien. Sie nehmen dann oft Kontakt zu externen Dienstleistern auf. Diese durchleuchten das Unternehmen und präsentieren Geschäftsführern am Ende eine digitale Vision. Das ist vernünftig. Dennoch gehen wir anders vor.
Welchen Ansatz verfolgen Sie als Strategieberater für die Digitalisierung?
Uns ist eine niedrige Flughöhe wichtig. Das heißt, dass wir auf dem Shopfloor agieren und die Sprache des Produktionsleiters sprechen. Wir zeigen also nicht gleich ein schlüsselfertiges Konzept, sondern erarbeiten es mit unseren Kunden zusammen. Währenddessen verstehen wir uns als Innovationspartner.
Dennoch ist der Weg in die Digitalisierung ein komplexer Prozess. Wie strukturieren Sie ihn?
Idealerweise gliedern wir ihn in sechs Phasen, die sich als sehr erfolgreich erwiesen haben. In Phase eins beobachten wir sehr genau und durchleuchten das Unternehmen. Dabei bietet sich Design Thinking an. Hilfreich ist ein interdisziplinäres Team, mit offenen Fragen aus Sicht der Anwender. So entwickeln wir erste Ziele und eine Strategie. Im zweiten Schritt checken wir sozusagen die Fitness. Wir machen eine Ist-Aufnahme in Bezug auf Mensch, Organisation und Technik: Wie fit ist die Organisation überhaupt hinsichtlich der Digitalisierung? Inwieweit sind Funktionen und Prozesse bereits vernetzt? Danach legen wir in einer Roadmap die Meilensteine fest. Sie priorisiert die Aufgaben auf Basis des jeweiligen Industrie-4.0-Reifegrades. In Phase vier sprechen wir über konkrete Technologien. Wir präsentieren verschiedene Lösungen, um das Problem im Unternehmen in den Griff zu bekommen. Danach geht es in den letzten beiden Phasen darum, anhand eines Prototyps die minimale Funktionsfähigkeit und Akzeptanz der Idee zu testen, bevor es dann final in der Linie realisiert und vervielfältigt wird.
Sie haben eine um-fassende Beratungsphase beschrieben. Gibt es auch Angebote, bei denen man sich Inspiration holt?
Wir wollen Kunden immer individuelle Wege in die Industrie 4.0 zeigen. Deshalb bieten wir unabhängig von diesen eben geschilderten Phasen eine Art Werkzeugkasten mit unterschiedlichen Workshop- und Bootcamp-Formaten an. Möglich ist zum Beispiel ein zurzeit noch kostenloser Readiness-Check oder eine Teilnahme am IT-Bootcamp-Hackathon, also einer kollaborativen Software- und Hardwareentwicklungsveranstaltung. Viele melden sich für unsere IoT-Bootcamps an unseren Firmensitzen in Schwerin und Stuttgart an. Hier laden wir im größeren Umfeld zu Themen wie 3D-Druck, Retrofit-Sensorik oder Robotik ein. Kunden können vor Ort einzelne Lösungen ausprobieren.
Welche Empfehlung geben Sie Unternehmen mit auf den Weg?
Wenn sie die Digitalisierung konsequent durchziehen, erreichen sie neue Zielgruppen und erzeugen und befriedigen neue Bedürfnisse. Weil das sehr komplex ist, warten noch zu viele Firmen ab und schauen, was der Wettbewerb unternimmt. Wir helfen unseren Kunden daher, diesen Prozess umzukehren. Unternehmen kommen mit unserem Sechs-Phasen-Modell vom Reagieren zum Agieren. Sie sind danach erfolgreicher Akteur in der digitalen Transformation.
Wie halten Sie als Strategieberatung in Sachen Digitalisierung und Industrie 4.0 Ihr Know-how auf dem neuesten Stand?
Wir kooperieren seit Jahren mit Hochschulen und Forschungseinrichtungen. Zu den engen Kontakten zählen beispielsweise die TU München und das Fraunhofer-Institut für Arbeitswirtschaft und Organisation IAO. Als SAP-Partner haben wir außerdem Einblick in die Firmen, die den SAP IoT Startup Accelerator durchlaufen.
INFORMATION
Unternehmen, die an kostenlosen und kostenpflichtigen Bootcamp-Formaten von Trebing + Himstedt interessiert sind, können sich über www.t-h.de, [email protected] oder Telefon +49 385 395 72-12 informieren und anmelden.