Jaguar Land Rover (JLR) produziert mittlerweile 70 Prozent seiner Modelle aus hochfestem Aluminium.
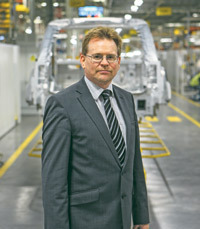
Dr. Mark White
Chefingenieur Karosseriebau bei Jaguar Land Rover
Die Limousinen Jaguar XE und XF besitzen bereits eine Vollaluminiumarchitektur. Im Interview: Dr. Mark White, Jaguar Land Rover Chefingenieur Karosseriebau.
Der Jaguar XE ist der erste Mittelklassewagen mit einem Aluminiumanteil von 75 Prozent. Warum fiel die Entscheidung auf das Leichtmetall?
Die leichte Aluminiumkonstruktion erlaubt es uns, die hervorragende Fahrleistung unserer Oberklassemodelle auch auf die Mittelklasse zu übertragen. Die Rohkarosserie wiegt dank der Aluminiumarchitektur nur 251 Kg und benötigt so deutlich kleinere Motoren, um die gewohnte Jaguar-Performance zu liefern. Mit einem CO2-Ausstoß von weniger als 100 Gramm schont der neue XE die Umwelt und bietet dem Fahrer gleichzeitig das volle Fahrvergnügen.
Durch die Verwendung von Aluminium-Rezyklaten, benötigen wir im Vergleich zur Primärmetallherstellung 90 Prozent weniger Energie.
Die Anzahl der in die Rahmenstruktur integrierten Bauteile spielt für die Kosten eine wichtige Rolle. Wie hält JLR die Anzahl der Bauteile gering?
Wir setzen bei der Produktion verschiedener Aluminiumbauteile auf Druckguss, um so eine maximale Integration selbst kleinster Bauelemente zu erzielen. Bei einem Federbeindom einer Aluminiumkarosserie beispielsweise ersetzt ein Gussteil sechs bis zehn Bauteile einer konventionellen Karosserie, auf jeder Seite. So lassen sich alleine an dieser Stelle zwölf bis 20 Teile einsparen.
Eine hohe Torsionssteifigkeit hat großen Einfluss auf die Fahreigenschaften. Wie sehen Sie das Verhältnis zwischen ganzheitlicher und lokaler Steifigkeit an kritischen Punkten mit hoher Krafteinwirkung?
Wir betrachten mehr als die komplette Karosseriesteifigkeit. Deshalb setzen wir auf ein ausgewogenes Verhältnis zwischen hoher Torsionssteifigkeit für die gesamte Karosserie und möglichst steifen Befestigungspunkten. Indem wir etwa den vorderen Federbeindom aus einem Guss fertigen, können wir die Stärke des Bauteils anpassen.
Auf diese Weise lässt sich die lokale Steifigkeit, in diesem Fall an der Vorderradaufhängung, deutlich erhöhen. Gepaart mit einer perfekten Achsverteilung von 50:50 und einem dank Aluminium gesenkten Schwerpunkt lassen sich das Handling und die Fahrdynamik optimal einstellen.
Zusätzlich spielt eine solide lokale Steifigkeit an der Radaufhängung auch für das sogenannte NVH-Verhalten (Noise, Vibration und Harshness – die Wertung der Innenraumgeräusche eines Fahrzeugs) und die übertragenen Resonanzen eine große Rolle.
Hinsichtlich NVH und Aerodynamik: Welche Vorteile bietet in diesem Zusammenhang die Aluminiumkarosserie?
Neben der lokalen Steifigkeit ist natürlich auch die Aerodynamik für ein gutes NVH-Verhalten verantwortlich. In Zusammenarbeit mit Designern und Aerodynamikern haben wir versucht, mit dem neuen XE und XF möglichst windschnittige und damit leise Autos zu kreieren.
Dabei herausgekommen ist ein cW-Wert von sagenhaften 0,26. Um solche Ergebnisse zu erzielen, simulieren wir den Großteil der Aerodynamik mittels modernster CFD-Software und nutzen den Windkanal lediglich, um die gewonnenen Ergebnisse abzusichern.
Inwiefern trägt die Karosseriestruktur zu dem hervorragenden Ergebnis beim Euro-NCAP-Crashtest bei?
Die Aluminiumkonstruktion absorbiert mehr Energie als eine vergleichbare Stahlkarosserie. Zum anderen gilt bekanntlich nach Newton: Kraft = Masse x Beschleunigung. Indem wir eine leichtere Karosserie entwickeln, reduzieren wir die bewegte Masse.
So verringern wir automatisch die in einen Unfall eingebrachte Energie und minimieren die Schwere des Crashs. Von der aluminiumintensiven Rohkarosserie bis zur hochmodernen Stereokamera als Herzstück des autonomen Notbremsassistenten wurden alle Systeme des XE und XF auf das höchste Sicherheitsniveau getrimmt.
Die Reparatur einer Aluminiumkarosserie nach einem Unfall erfordert aufgrund des sensiblen Materials spezielle Maßnahmen. Wie unterstützt JLR seine Kunden im Schadensfall?
Der entscheidende Faktor bei einer Reparatur ist weniger das Material, es sind die hohen Arbeitskosten. Also sorgen wir mit einer leicht austauschbaren Frontpartie dafür, dass der Wagen zum Beispiel bei Auffahrunfällen schnell und einfach zu reparieren ist. Solche Reparaturen der sogenannten Kategorie B kann jeder lokale Jaguar Land Rover Händler ausführen.
Schließlich haben wir und unsere Händler seit 2003 Erfahrung mit Aluminiumkarosserien. Bei schwereren Schäden der Kategorie A leitet der optimal vernetzte Händler das Fahrzeug an regionale Werkstätten weiter, die über die entsprechenden Mittel verfügen, selbst strukturelle Beschädigungen zu beheben.
Eine Weltpremiere feiert im XE und XF die hochfeste Legierung RC 5754, die beinahe vollständig aus recyceltem Aluminium besteht. Worin liegen ihre Vorteile?
Indem wir fast ausschließlich Aluminium-Rezyklate für die Legierung verwenden, benötigen wir im Vergleich zur Herstellung von Primärmetallen 90 Prozent weniger Energie. Damit optimieren wir schon in der Produktion die CO2-Bilanz des Fahrzeugs und schonen die Umwelt.
Bis zum Jahr 2020 wollen wir den Anteil recycelter Metalle im Fahrzeug auf 75 Prozent steigern und so die Rentabilitätsschwelle von jetzt 40.000 auf 18.000 Kilometer senken. Ab einer Laufzeit von etwa sechs Monaten wäre der Wagen damit „kohlenstoffneutral“ und würde den Rest seines Lebenszyklus CO2 einsparen.
Während bei JLR Aluminium und dessen Recycling eine große Rolle spielen, setzen manche Wettbewerber weiterhin auf Stahl. Wie beurteilen Sie die Entwicklung?
Stahl ist nach wie vor ein günstiger und zuverlässiger Werkstoff. Mit Aluminium hingegen lässt sich eine Gewichtsersparnis von 40 Prozent erzielen. Ich schätze allerdings, dass Fahrzeuge der Klasse A und B zumindest in den nächsten Jahren noch bei der günstigeren Lösung Stahl bleiben.
Sie erfüllen aufgrund ihrer geringen Größe und Motorisierung teilweise schon heute die CO2-Vorgaben für 2020 und können so zunächst auf Leichtbaumaßnahmen verzichten. Im Gegenzug halte ich es im C- und D-Segment für nahezu unmöglich, mit konventionellen Stahlkarosserien und Motoren die CO2-Marke von 100 Gramm zu unterschreiten.
Das heißt, Sie sehen in Zukunft Aluminium als den Nachfolger konventioneller Stahlkarosserien und nicht etwa Carbon?
Ein wichtiger Faktor beim Wechsel von Stahl zu einer aluminiumbasierten Leichtbaustrategie ist der, dass ein Großteil der vorhandenen Fertigungsstationen, wie das Presswerk oder die Lackieranlage, erhalten bleiben kann. Lediglich kleine Anpassungsmaßnahmen wären nötig, wie der Austausch von Punktschweißzangen gegen Nietpistolen. Bei der Produktion eines Fahrzeugs aus Carbon werden alle diese Stationen unbrauchbar.
Zusätzlich liegen die Kosten selbst bei besten Produktionsbedingungen fünf- bis zehnmal höher als bei Aluminium. Auch bei einer voll integrierten Lieferkette macht der unveränderliche Preis des Rohmaterials rund 50 Prozent der gesamten Produktkosten aus. Darüber hinaus ist Carbon eine ölbasierte Technologie – und bei den knappen Ressourcen müssen wir uns entscheiden, ob wir die Fahrzeuge antreiben oder ob wir sie bauen möchten.
Wäre denn in Zukunft auch eine Karosserie aus 100 Prozent Aluminium denkbar?
Ein klares Ja, denn das können wir unseren Kunden bereits heute anbieten: XE und XF bestehen zu 75 Prozent aus dem Leichtmetall, und mit den neuen F-TYPE- und XJ-Modellen sowie dem Range Rover und Range Rover Sport bieten wir bereits Modelle aus nahezu 100 Prozent Aluminium an. Um in Zukunft auch auf diesen geringen Stahlanteil zu verzichten und trotzdem maximale Stabilität zu gewährleisten, entwickeln wir unsere Fügeprozesse kontinuierlich weiter.
Nach langen Versuchsreihen verfügten wir beim Erscheinen des XJ im Jahr 2002 über ein voll funktionsfähiges und leistungsstarkes Fügeverfahren. Dieses ermöglicht uns heute ein hohes Produktionsvolumen mit optimalen Zykluszeiten. Seitdem hat die Entwicklung nicht haltgemacht. Betrug die Zykluszeit für den XJ im Jahr 2002 von Station zu Station noch sechs Minuten, liegt sie beim Jaguar XE und XF heute bei gerade einmal 70 Sekunden. Ein Unterschied wie Tag und Nacht.