Ein Gespräch mit Kai Kisseberth, Geschäftsführer csi entwicklungstechnik, über ein neues Fahrzeugsitzkonzept, die digitale Prozesskette auf dem Weg dahin und einen Ultraleichtbausitz, der viel Marktpotenzial hat für künftige Hypercars, Ultraleichtbaufahrzeuge und Lufttaxis.
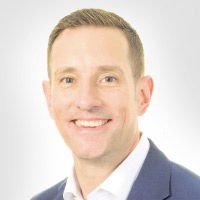
Kai Kisseberth
Geschäftsführer csi entwicklungstechnik GmbH, Neckarsulm
Sie haben zusammen mit anderen Industriepartnern in sieben Monaten einen Ultraleichtbausitz produziert und in diesem Jahr präsentiert. Können Sie das Produkt näher beschreiben?
Das Ziel war, mit neuen Technologien einen Sitz ganz neu zu denken. Wir haben auf diese Weise ein Fahrzeugsitzkonzept mit einem Gewicht von zehn Kilogramm komplett neu konzipiert. Hierbei gab es zwei entscheidende Erfolgsfaktoren. Zum einen der Einsatz der digitalen Prozesskette, einer Methodik für eine agile und effiziente Entwicklung. Zum anderen die Verwendung der innovativen xFK-in-3D™-Technologie Damit haben wir die Leichtbauphilosophien „die richtigen Materialien am richtigen Ort“ sowie „nur so viel wie benötigt“ perfekt umgesetzt. Das Ergebnis, unser Ultraleichtbausitz, stellt uns alle sehr zufrieden, da wir alle gesetzten Ziele erfüllt haben. Das haben uns auch viele Kunden bei Terminen bestätigt. Außerdem sind wir sehr stolz darauf, zwei German Innovation Awards und den Altair Enlighten Award – quasi den „Oscar“ des Leichtbaus – gewonnen zu haben. Für die csi entwicklungstechnik GmbH ist der wichtigste Faktor an diesem Projekt, dass wir die digitale Prozesskette etabliert haben.
Können Sie das Prinzip der digitalen Prozesskette in Verbindung mit xFK in 3D™ näher erläutern?
Bei der digitalen Prozesskette arbeiten die unterschiedlichen Entwicklungsbereiche wie CAE-Simulation, CAD-Konstruktion sowie CAS, also Computer Aided Styling, sehr eng zusammen. Die CAE-Simulation hat dabei das Lead in der Entwicklung. Zu Beginn haben wir Lastkollektive und Lastpfade einer Struktur definiert. Diese sichern wir dann durch statische und dynamische Berechnungen ab.
xFK in 3D™ beschreibt einen ebenso konkreten wie messbaren technologischen Beitrag zu integrativem Leichtbau der Zukunft. Wenn die Glas-, Kohle-, Basalt- und viele weitere Naturfasern von Verbundwerkstoffen – also xFK – nach den gewünschten Bauteilfunktionen und Lastkollektiven ausgerichtet und dreidimensional gefertigt werden, also in 3D, entstehen räumliche, ultraleichte Strukturbauteile hoher Intelligenz.
Bei der Prozessinnovation xFK in 3D™ handelt es sich um eine hochflexible, nahezu beliebig gestaltbare, kostengünstige und nachhaltige Faserverbundtechnologie, um Bauteile zu wickeln. Mit ihr sind bereits unterschiedlichste Produkte beziehungsweise Anwendungen für verschiedene Branchen und Marktsegmente realisiert worden.
Welche Vorteile haben Ihre Kunden davon?
Der Einsatz der digitalen Prozesskette ermöglicht eine sehr effiziente Entwicklung. Die Time-to-Market kann verkürzt werden. Das Produkt kommt entsprechend schneller auf den Markt. Des Weiteren können unsere Kunden, zumindest teilweise, auf den Einsatz von physischen Prototypen verzichten.
Welches Marktpotenzial sehen Sie darin?
Die digitale Prozesskette funktioniert! Dies haben wir mit der Entwicklung des Ultraleichtbausitzes in einer sehr kurzen Zeitschiene von sieben Monaten mit acht beteiligten Partnern bewiesen. Somit können wir die Methodik auf weitere Fahrzeugkomponenten übertragen. Des Weiteren sehen wir, speziell auch in Verbindung mit der xFK-in-3D™-Technologie, Marktpotenzial bei der Entwicklung von hochperformanten Fahrzeugen – Hypercars – wie auch zukünftigen hybriden intermodalen, fliegenden und fahrenden Lösungen wie Lufttaxis oder dergleichen. Außerdem ist es spannend für Ultraleichtbaufahrzeuge, Hubschrauber, Mikromobilität, Multicopter und allgemein für die Luftfahrtbranche. Man kann nach heutigem Stand der Technik und Wissenschaft nicht leichter bauen als auf Faserverbund-Einzelstrangebene, zum Beispiel mit dem von uns genutzten xFK in 3D™.